It’s not a lie that running an organized warehouse can be very costly. You need to consider everything from equipment, staff and other operational costs. It’s very prudent for warehouses to run efficiently. Warehouse managers have the important responsibility of optimizing the warehouse space to increase the stock in storage. That way, it can be moved or located effortlessly and safely.
Running a warehouse requires innovative thinking, new technology, and logistical knowledge. Below are some of the best ways to maximize any available warehouse space. On the supply chain. You are likely to face the challenge of managing inventory in your distribution center or warehouse. In most cases, there is very limited space. A regular distribution center runs out of space at about 85%.
Note that this is not the storage area only but also the shipping, receiving and other process areas in the warehouse. If there isn’t enough space for inventory in the distribution center, there are a few ways to increase capacity. Here’s what you need to know.
Increase The Aisle Width
Source: Pexels
The available space in an organized warehouse depends on the aisles available in the warehouse. If you have not optimized the aisles properly, you could be losing out a lot of money. You can correct this very fast. Start by removing any wasted space to increase the number of aisles present. Also, you can reduce the pallet racks accordingly thus increasing the overall stock available in the warehouse.
Depending on the size of racks and the type of products you are stocking, you can reduce the aisle width by half and increase your storage space by at least 50%.
When considering the optimal aisle width, you should check a few factors. For instance, you might be using large forklifts that might pose a challenge to the aisle width. Note that, these large forklifts will not fit comfortably in the smaller space with enough room to handle the processes. You should also consider the staff who might be working in the aisles. As a result, the optimum aisle width will be different for each operation. Take the right measurements for the entire warehouse and consider all the aspects that need to fit into the aisle.
Try Cross Docking
With cross-docking, the warehouse can minimize the storage space in use by receiving then sorting and scanning the inbound stock at a chosen terminal. Next, the stock will be loaded into the outbound trucks and the vehicles without requiring any storage.
As a result, the stock will not be stored unnecessarily before it reaches the final destination. Actually, it will be sorted faster and placed back into the distribution chain. It might be tough to manage the logistical technique but it will actually save a lot of space for those looking to invest in the best resources.
Consider The Upward Potential
Source: Pixabay
If you have very little to no floor space left, you need to start thinking upwards. Currently, there are numerous shelving options with vertical storage options. It’s a good way to increase your overall capacity without worrying about floor space. With these options, you can go as high as 1 foot or 10 feet depending on your storage needs.
Before adding more tiers, you need to consider how the stock placed in the higher levels will be transported. You need to plan for everything including locating, removing and delivering the stock from the top tier. That way, you can avoid any surprises when you realize your forklifts can’t actually reach the top shelves. Basically, you need to be prepared for everything.
Organize Supplier And Offsite Storage
Inventory management in any warehouse is critical. If you are stocking up on items that haven’t been purchased yet, you could be using a lot of space that should be left for quick moving goods. You need to consider offsite storage and leave the primary warehouse to store the ready orders. That way, you can streamline your operation and separate your overall stock.
It will be easier to locate and manage the stock this way. There are also suppliers who offer storage space for any excess stock, especially packaging materials. They are ready to store the stock on site and deliver weekly shipments. That way, you can avoid any excess stock or unused stock in the warehouse for long periods.
Additionally, you should be able to decrease or increase your incoming orders thus gaining the required flexibility per week. Of course, you should remember that each warehouse is different. Whether it’s the stock, logistical considerations and much more, you need to think of the best ways to optimize your warehouse space. It’s tough purchasing a new warehouse or relocating to a new lot so you need to take advantage of what’s available.
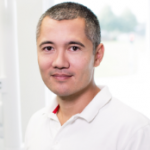
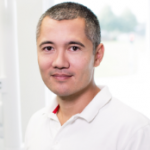
Latest posts by Michael Phillips (see all)
- 4 Perfect Ways on How to Maximize your Available Warehouse Space - August 6, 2019
- 14 Features You Should Consider To Add In Your Home - July 29, 2019
- Deciding Which Is The Best For Business Between A Color Copier And Multifunction Printer - July 21, 2019
Visitor Rating: 5 Stars
Visitor Rating: 4 Stars
Visitor Rating: 5 Stars
Visitor Rating: 5 Stars
Visitor Rating: 4 Stars